Lelassít a Toyota, hogy gyorsabban gyárthasson

Újabb forradalmi eljárást honosíthat meg az autóiparban a Toyota. Ezúttal a versenyautó-építés folyamatát gondolták újra: az innovatív gyártási technológia jóvoltából három hét helyett három nap alatt végezhetnek egy projekttel.
Szeptember utolsó napjaiban történelmi pillanatnak lehettek tanúi a Super Taikyu széria ötödik körének nézői és résztvevői. A suzukai versenypályán lezajlott futam számos indulója között ott volt egy, látszólag átlagos Toyota GR Yaris is, amelyről csak a beavatottak tudták, hogy a motorsport jövőjét képviseli.
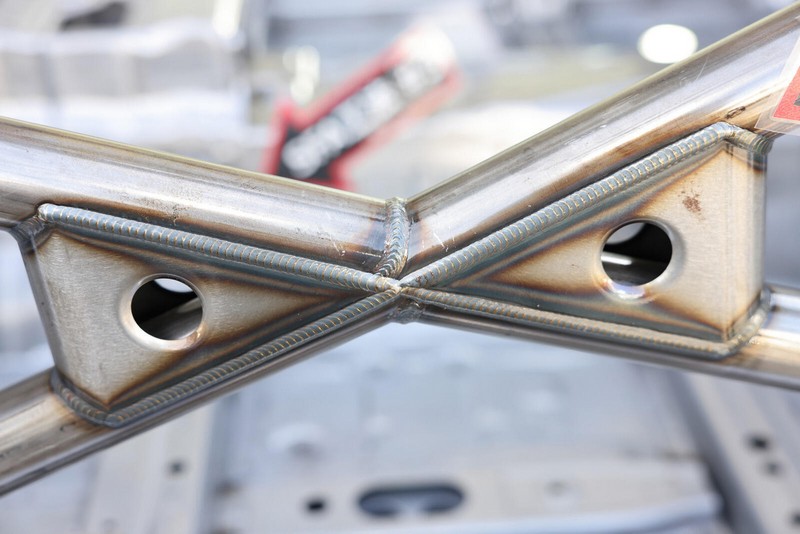
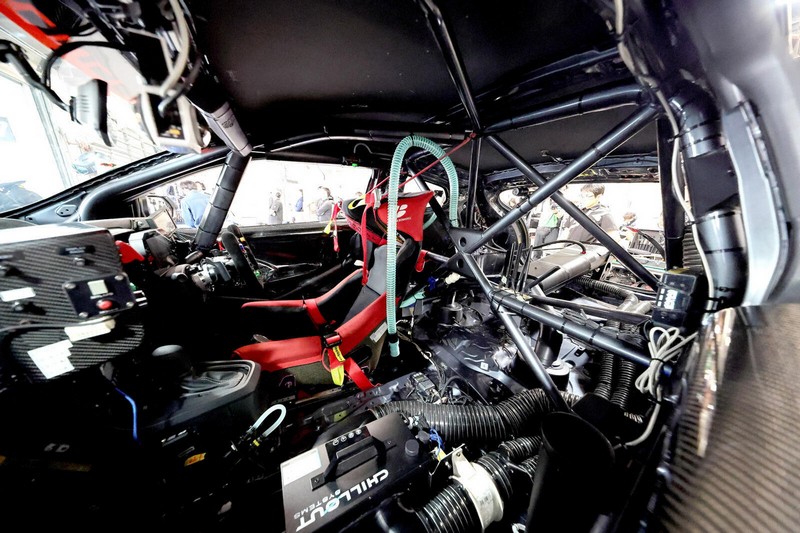
A 32-as rajtszámú autó nem hajtásláncában, nem is futóművében vagy üzemanyagában volt különleges – pedig a Toyota mindegyik téren komoly fejlesztéseket tett már le az asztalra. A kis GR Yarist bukócsöve tette egyedülállóvá, pontosabban az a gyártási eljárás, amely egyelőre kísérleti fázisban jár, ám ha beválik, nagyságrendekkel csökkentheti a versenyautó-építés időtartamát és azzal együtt költségeit.
A történet 2023 augusztusában, Finnországban kezdődött, ahol Tojoda Akio meglátogatta a márka ralicsapatának boszorkánykonyháját. A Toyota Gazoo Racing World Rally Team (TGR-WRT) szerelői épp egy bukókeret beépítésén fáradoztak – a szóválasztás nem véletlen, hiszen hagyományosan ennek a biztonsági és merevítési feladatokat egyaránt ellátó szerkezetnek a beillesztése a versenyautó-építés egyik legkényesebb, legproblémásabb fázisa.
A GR Yaris bukókeretét mintegy négy tucat csőből hegesztik össze. A munka nagy pontosságot és még több időt igényel: átlagosan két-három hétig tart, amíg a helyükre kerülnek az elemek. Ezzel nincs is gond a szezon kezdetén, ám ha egy autó olyan mértékben sérül meg, hogy ki kell cserélni, megkezdődik a versenyfutás az idővel: vajon elkészülnek-e a munkával a következő futamra, máshonnan kell átcsoportosítani egy autót, vagy a versenyzőnek ki kell hagynia a ralit?
Tojoda Akio arra kérte munkatársait, találjanak megoldást a problémára. A projektet a GR járműfejlesztési részlegének igazgatója, Kavakita Acusi vette kézbe, a megoldás azonban nem adta magát azonnal. A bukókeret összeállítása ugyanis valóságos művészet: a hegesztéssel járó hőfejlődés hatására alak- és méretváltozáson mennek keresztül a csövek. Egy takumi hegesztőmester ezzel tisztában van. Több évtizedes tapasztalata birtokában pontosan tudja, milyen mértékű torzulással számolhat, és ezeket szinte ösztönösen ellentételezi a munkavégzés során. Ezt a szintű kézműves tudást lehetetlen átadni egy robotnak – vagy mégsem?
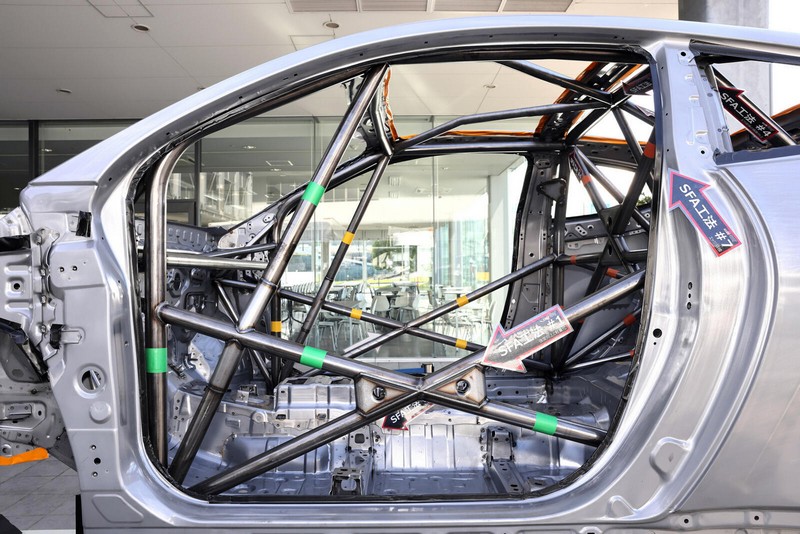
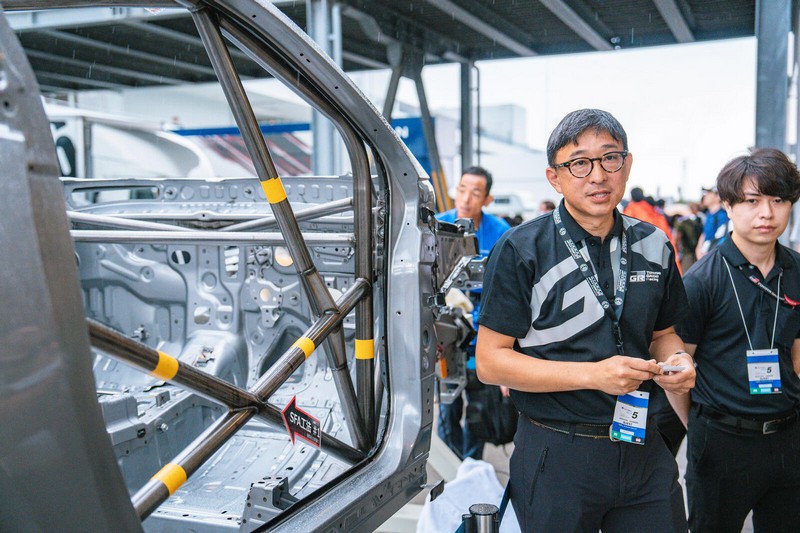
Ezen a ponton kérték fel tanácsadónak Sibata Sotát, az ipari robotokat gyártó Yaskawa Electric Corporation robotikai szakértőjét, akinek egyetlen kérdést tettek fel: hogyan hegeszthet egy robot alakváltozás nélkül? Lelkes amatőr autóversenyzőként Sibata-szan személyes küldetésnek tekintette a feladatot, és csakhamar készen állt a válasz: le kell lassítani a robotokat, hogy az anyag a folyamat egyetlen pontján se lépje át a kritikus hőmérsékletet.
Ez első hallásra egyszerű feladatnak tűnhet, ám a teljes folyamatot újra kellett gondolni. Hosszas kísérletezés után azonban megszületett a fázisaiban megszakított ívhegesztés (Sequence Freezing Arc-welding, SFA) technológiája, egy olyan, világelső eljárás, amely nem várt járulékos előnyöket is hozott magával.
Az SFA-robotok a Toyota mesterhegesztőinél is lassabban dolgoznak, az eredmény azonban rendkívüli. Az így kapott hegesztési varrat vékonyabb, de szélesebb – összességében 25 százalékkal könnyebb egy sztenderd varratnál, viszont mélyebbre hatol a hegesztett anyagban, ezért aztán 10-25 százalékkal erősebbé teszi az érintett alkatrészt.
Ez jól hangzik, csakhogy a feladat az volt, hogy felgyorsítsák a munkát, ne pedig tovább lassítsák. Az SFA-eljárás során azonban minden lépésnél megvárják, hogy az olvadt fém elkezdjen megszilárdulni: a megolvadt acél mennyisége soha nem lesz akkora, hogy saját súlyánál fogva megfolyjon. Így tetszőleges irányban és pozícióban elvégezhető a hegesztés, ráadásul olyan területeken is bevethető az eljárás, ahol korábban csak ponthegesztést alkalmazhattak.
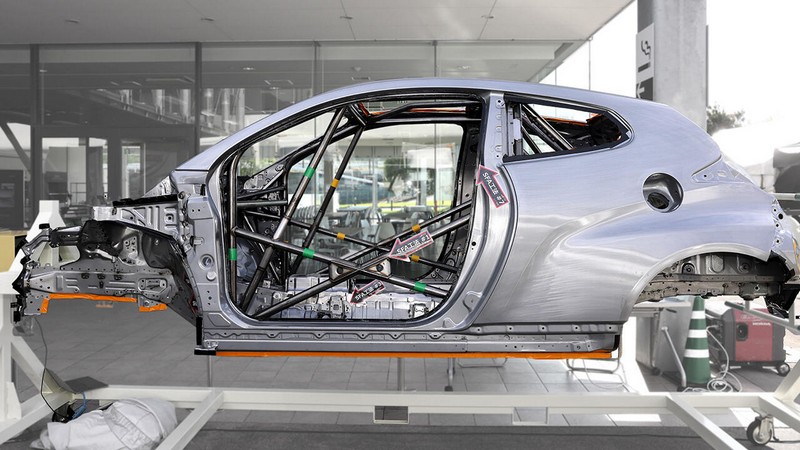
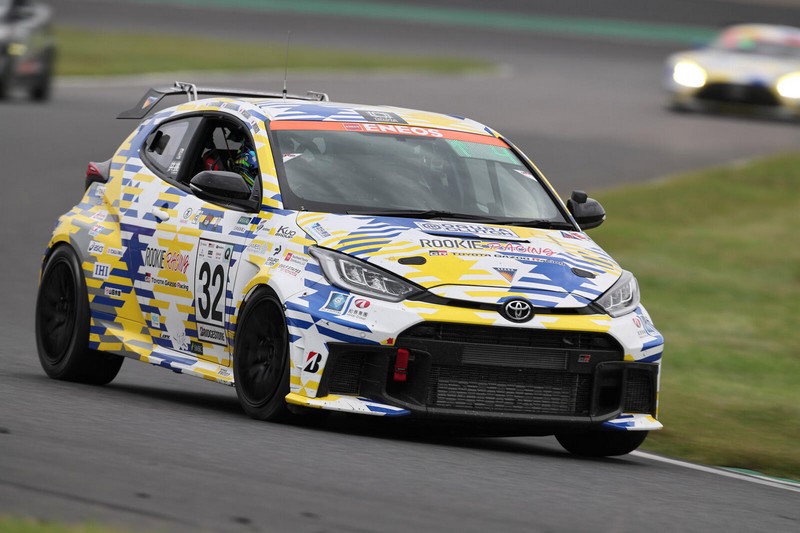
Az időmegtakarítás pont itt jelentkezik. Míg korábban az autó belsejében, kézzel állították össze a bukókeretet, ami egy két- három héten át tartó folyamat volt, most három, gyorsan elvégezhető fázisra bontják a gyártást. A gyárban elkészítenek három különálló modult (ez egy napig tart), majd ezeket a térbeli szerkezeteket másfél napnyi munkával összeigazítják az autó belsejében – természetesen minden milliméteres pontossággal passzol –, és végül a három elem illesztési pontjait fél nap alatt összehegesztik egymással és az autó karosszériájával.
Jól mutatja a feladat komplexitását, hogy a pontos illesztés ugyanannyi időt vesz igénybe, mint maga a hegesztés – pontosan ez viszi az időt a takumi mesterek számára, akiknek szűk térben kell nem három, hanem negyven elemet egymáshoz igazítaniuk.
Miután a gyárban elkészültek az első prototípusok, ideje volt próbára tenni azokat. A Toyota versenyzői azonban elégedetlenek voltak: a GR Yaris túlságosan merev lett. Hagyományosan a vázszerkezet bizonyos mértékű torziós és flexiós lágysága kompenzálja a futóműre ható erőket, itt azonban ez a hatás elmaradt. A mérnökök innen tudták azonban, hogy működik az eljárás: egy különösen merev karosszériában ugyanis sokkal pontosabban állítható be a futómű – magyarul az autó minden esetlegességet kiküszöbölve, hajszálpontosan olyanra hangolható be, amilyennek a pilótája szeretné, vagy az adott verseny útviszonyai szükségessé teszik. Arról nem is beszélve, hogy a hegesztési varratok számának vagy hosszának csökkentésével mérsékelhető a szerkezeti szilárdság – fordítva azonban már sokkal nehezebben menne a fejlesztés.
Újabb gyártási folyamatban teszi tehát feleslegessé tapasztalt szakembereit a Toyota, vélhetnék a kritikusok, ám ez pont fordítva van. A gépi gyártással ugyanis elkerülhetetlenek bizonyos fokú pontatlanságok. Ezeket egy átlagos autóvezető észre sem venné, ám a Toyota pilótái pontosan érzik, hogy a GR Yaris nem úgy viselkedik, ahogy kellene. Ezeket a pontatlanságokat pedig kizárólag emberi odafigyeléssel, tapasztalattal és érzékkel lehet kijavítani – a hegesztő mesterek tudását tehát a jövőben magasabb szinten kamatoztathatja a Toyota, még tökéletesebbé téve a motorsport legmagasabb szintjére szánt versenyautóit.
Ami pedig az alacsonyabb kategóriákat illeti, ott közvetlenül érvényesülhetnek a robotizált gyártás kézzel fogható előnyei: a versenyautók megfizethetőbbek lesznek, és gyorsabb ütemben lehet azokat gyártani, így összességében többen engedhetik meg maguknak, hogy a Toyota Gazoo Racing autóival versenyezzenek – a fejlesztés tehát a motorsport minden szintjén előrelépést tesz lehetővé.
Fotók: Toyota, YouTube